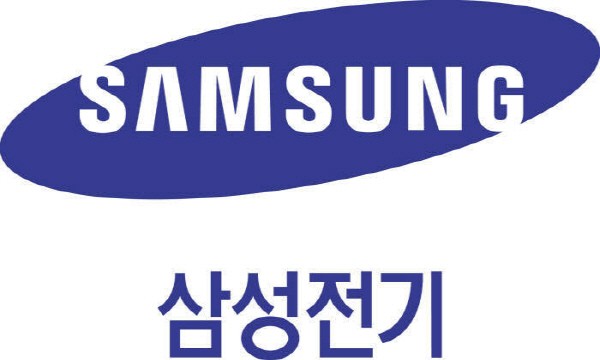
On the 15th, at Samsung Electro-Mechanics' Busan plant in Gangseo-gu, Busan, which produces flip chip-ball grid arrays (FC-BGA). To enter this place, I had to wear a full-body dust-proof suit and press down on a hat to keep my hair from falling out. Even sunscreen was not allowed, so I had to wash my face with a cleanser before entering. Only after washing the dust-proof shoes with water once more and going through the 'air shower room', was I able to step into the FC-BGA production plant.
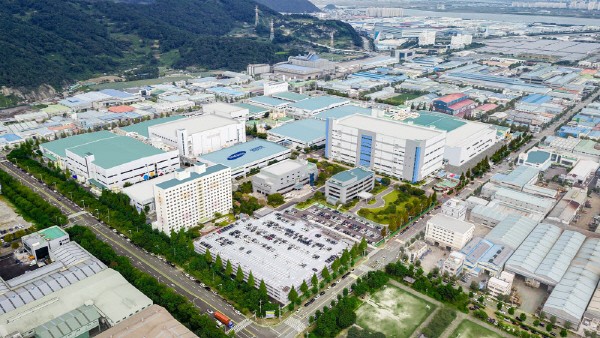
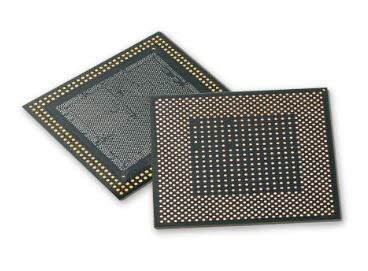
I arrived late Thursday afternoon during the scorching summer vacation at Samsung Electro-Mechanics' FC-BGA production building, which was operating without a single machine on pause. I couldn't hear what the person next to me was saying without the use of a microphone. Despite the sluggish global economy and the shrinking parts market, FC-BGAs have became a "core component that can't be sold because they're all gone," and all production lines were operating at full capacity. The package substrates produced by Samsung Electro-Mechanics last year was equivalent to the area of 100 soccer fields.
FC-BGAs are a semiconductor substrate that connects semiconductor chips to the main substrate. It protects the semiconductor from external impact. If you compare semiconductor chips to the brain, the semiconductor substrate is the skull that protects the brain. It is also the blood vessels that carry information from the brain to each organ. FC-BGAs are mainly used in central processing units (CPU) and graphic processing units (GPU) such as PCs, servers, and networks. The popularity of FC-BGAs has soared to the point that demand cannot keep up with supply as demand for non-face-to-face has exploded and semiconductor processes have advanced.
All throughout the production building, the words 'war on dust' and 'we lose customer trust with a single particle' could frequently be seen. A company official stressed that visible dust are already huge particles of dust, and that invisible dust should also be caught. FC-BGAs requires 'clean rooms' that are comparable to that of a semiconductor factory. Even if a tiny amount of dust is found, the board must be discarded. It is a highly important issue linked to yield, customer trust, and cost.
Samsung Electro-Mechanics' Busan plant, the largest semiconductor package substrate production base in Korea, serves as the 'mother factory' for FC-BGAs. The Busan plant oversees FC-BGA research, development, and production. Recently, production in Vietnam is also expanding. The Sejong plant is also in charge of substrates.
In June, Samsung Electro-Mechanics made an additional investment of KRW 300 billion to build semiconductor package substrate (FC-BGA) facilities at its domestic Busan, Sejong, and overseas Vietnamese production subsidiaries. It has made a large-scale investment worth trillions in its substrate business, starting with an investment of 1 trillion won in Vietnam in December of last year.
Samsung Electro-Mechanics' decision was made based on its confidence in possessing the world's best microfabrication and microcircuit technology. FC-BGAs requires the highest level of technology to the point that it is called 'the finest of boards'. There are only a few companies in the world that can properly operate FC-BGA businesses. Among FC-BGAs, the server substrate technology is the highest, and Samsung Electro-Mechanics has also secured this technology. It will also be able to mass produce soon.
As the number of functions of electronic devices increases, the number of parts required also increases, which means the amount of circuitry required for signal transmission increases and becomes more complex. The substrates are stacked in several layers, since several circuits need to be made within a limited substrate area. The hole that connects each layer is called a Via, and the core technology is to drill a hole the size of 50 micrometers (㎛) within an area of 80 ㎛without a single error. Samsung Electro-Mechanics has secured the world's best technology to implement 10㎛ level Vias, which is one-tenth the thickness of A4 paper.
Samsung Electro-Mechanics plans to significantly expand its FC-BGA business in the future. They have managed to secure the technological prowess and their market position is positive. While domestic business sites such as Busan and Sejong play a central role, investments will also be expanded in their Vietnamese business sites, which are specialized for production.
An official from Samsung Electro-Mechanics said, "We will maintain our technological gap through large-scale preemptive investments, with our Busan plant specializing as a production base for high-end products, and we will enhance the competitiveness of our package substrate business."
Busan=
By Staff Reporter So-ra Park srpark@etnews.com