Semiconductor equipment industry is making an impressive effort in localizing etching and polishing equipment that are dominated by American and Japanese companies. These equipment are major equipment of front-end semiconductor processes. If they are able to localize them, they will be able to make hundreds of millions of dollars in profit.
According to related industry on the 18th, SEMES had made an outstanding performance last year in etching equipment market, which was a new business for SEMES. This company’s major processing equipment is in cleansing and it has been doing R&D on etching equipment for many years. It has finally started to make sales starting from last year, and industry is estimating that SEMES’ etching business has grown tremendously as more than 10% of its annual sales had come from etching equipment. Etching is a process that shaves off thin film, which is obtained by either a circuit pattern that is caused by exposure or deposition process, by using chemical or physical reactions. SEMES, which had made sales in physical etching equipment last year, is also planning to supply chemical etching equipment in the future. RAM Research from the U.S. currently holds more than 50% in shares in etching equipment market and holds the number 1 title. Followed by RAM Research are Tokyo Electron (TEL) and Applied Materials (AMAT) with 30% shares each.
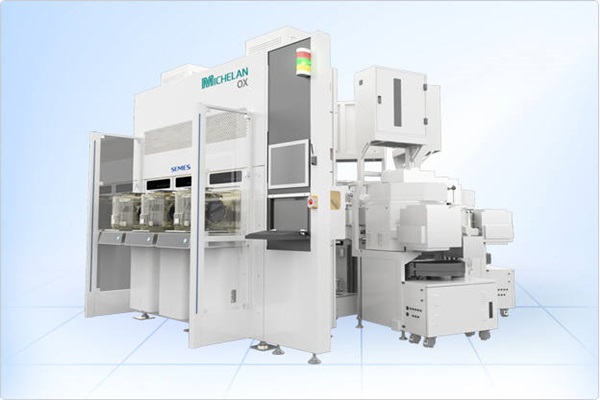
KC Tech, which has business centered on semiconductor wafer cleansing equipment, had also supplied demo CMP (Chemical mechanical polishing) equipment to its new customer’s new facilities at the end of last year. It is expecting that its supplies will not only increase for previous customers but also for new customers. CMP is a process that compresses surface of wafers onto pads, lets either oxide or metal abrasive flow through in between, rotates pads in fast speed, and flattens insulator films or metal wirings. Currently AMAT holds the number 1 title with more than 50% shares in this market. Although KC Tech is currently supplying basic equipment such as CMP, it is focusing on R&D with a mindset of supplying CMP equipment for tungsten, copper, and oxides that have high-added values.
PSK, which is the number 1 company in ashing equipment that eliminates photoresist residue after exposure, had finished developing etch back equipment and is starting to focus on winning orders from its customers. Etch back can form any kind of pattern by using a difference in selectivity of etching of deposited membranes without any help from exposure process. Although it cannot implement very fine patterns, its strength is its high productivity. Etch back market is shared by AMAT and TEL.
“South Korean equipment industry’s etching and CMP equipment were not made in one day but it had taken 5-7 years of development process to make them.” said a representative for Korea Semiconductor Industry Association. “It is encouraging to see the possibilities of South Korean equipment industry making profits in etching and CMP equipment that are monopolized by foreign businesses and gaining competitive edge in equipment industry.”
“Because front-end process equipment that South Korean businesses are pushing for still lacks quality and perfection compared to foreign equipment businesses, we still need to develop our technologies consistently.” said a representative for equipment industry. “We also need to prepare for lawsuits that foreign businesses might file against us on patents when we secure certain level of shares in this market.”
Staff Reporter Han, Juyeop | powerusr@etnews.com